Design for manufacturing (DFM) principles can help medical device manufacturers reduce costs, improve quality and launch products faster. Here’s a real-life example of how the team at Pulse Technologies applied DFM principles to achieve high-impact results for a medical device customer.
Customer Challenge
Medical device startup EndoEvolution was developing a new suturing device. The innovative product being developed used a formed circular needle to aid surgeons in minimally invasive surgeries.
The EndoEvolution team was comprised of a team of R&D engineers and a doctor. They had developed an innovative design concept for their product. They were now looking for a trusted partner to launch their product. Being a small team with no-inhouse manufacturing, they were looking for a partner who:
- Had R&D and manufacturing expertise to work as an extension of their design team to optimize product design for manufacturing
- Could improve unit level profitability by reducing manufacturing costs
- Could analyze the design and manufacturing process to minimize potential errors
- Had the ability to consistently produce high-quality products with repeatability, reproducibility, and low rework
- Had a robust Quality Management System (QMS) in place with in-depth expertise in US FDA’s design control requirements (21 CFR 820) and current good manufacturing practices (CGMPs)
After interacting with Pulse’s talented team and reviewing our state-of-the-art design and manufacturing capabilities, EndoEvolution partnered with us to help them achieve their objectives.
The PULSE Approach
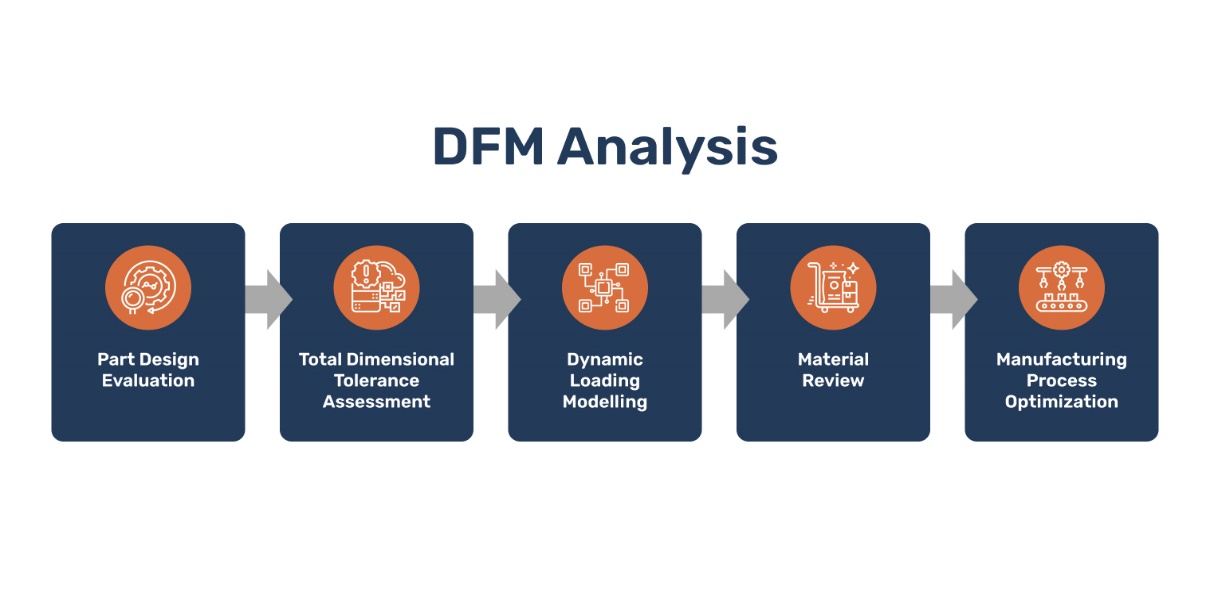
image: Pulse Technology robust DFM analysis process
Pulse’s cross-functional team with in-depth expertise in design and manufacturing analyzed the existing part design as a first step. The ability to reduce costs and improve quality lies in effective design for manufacturing modeling. This helps optimize both material costs as well as conversion (manufacturing costs).
The Pulse Technologies team conducted a complete DFM review of the design:
- Analyzed the dynamic loading through 3D modeling in Solidworks
- Conducted a total dimensional tolerance assessment
- Evaluated the manufacturing process based on product design and material selection
DFM Observations
Our in-depth DFM analysis indicated that:
he part design was not optimized for cost-effective manufacturing
There were improvement opportunities in the product design and component details to ensure easier manufacturability. Our analysis indicated opportunities to reduce assembly components, eliminate fasteners and more difficult assembly, and redesign fixtures. This would help reduce the cost, improve machining capability and reduce cycle times.
Quality and Reliability could be improved with better tolerancing of part fit and finish
Our total dimensional tolerance assessment indicated opportunities to improve reliability and ensure long-lasting usage. Our detailed tolerance analysis involved evaluating minimum, maximum, and nominal tolerance conditions.
Material selection needed to change
Our dynamic loading analysis using 3D modeling indicated the need to revisit the material chosen. Dynamic analysis provided great insights that could prevent potential failures in day-to-day usage. It simulated more real-life scenarios where loads on a part change with time and frequency and are not applied slowly. We were able to understand the response of the model to the loading conditions.
Our analysis indicated that the design of some components did not account for the maximum loading of the system. We then reevaluated materials based on the loads and stresses of the components.
We presented the results of our detailed DFM analysis to the EndoEvolution team and worked with them to incorporate the changes into the product design.
Customer Impact
Application of DFM principles by the Pulse Technologies team resulted in:
- 20% reduction in assembly components from what was proposed in the original design
- 21% reduction in manufacturing costs
- Significant improvement in quality and reliability of the product
- High levels of end-customer satisfaction – great feedback was received from surgeons using the product
- No product returns due to design and manufacturing issues
At Pulse Technologies, we offer:
- 25+ years of medical device manufacturing experience.
- Industry-leading in-house metrology and testing capabilities
- 70,000 sq.ft facility.
- 100+ CNC machine tools.
- Data conveniently formatted for DHFs/DHRs, and much more.
Want to learn more? Get in touch: sales@pulsetechnologies.com.